Troubleshooting scaling-up issues from coupons to parts - P134
Troubleshooting scaling-up issues from coupons to parts | |||||||
---|---|---|---|---|---|---|---|
Practice document | |||||||
Document Type | Practice | ||||||
Document Identifier | 134 | ||||||
Themes | |||||||
Tags | |||||||
Objective functions |
| ||||||
MSTE workflow | Troubleshooting | ||||||
Prerequisites |
Q: "I have made lots of good quality flat panels during qualification but my parts, cured in the same way (and perhaps using the same cure program), are of poor quality. How can I make the quality of my cured parts similar to my coupons?"
A: Conceptually, a test specimen cut out from any location in a composite structure should have the same chemical, physical, and mechanical outcomes as the specimens that were used during development of both material and structure. This only occurs as the successful result of a controlled manufacturing process that is capable of achieving the same outcomes in production as was achieved during the material and process development phase.
A fundamental concept in materials science is that process history leads to microstructure evolution, which in turn determines quality as well as mechanical and functional properties. Ultimately the goal is to control the interactions of the material, shape, tooling & consumables, and equipment (MSTE) so that the process history in the part is as close as possible to how the process history was in the coupons. When going from coupons to parts, the material will stay the same, so this means adjusting only shape, tooling & consumables and equipment in order to keep the process history (thermal history, pressure history, vacuum history, etc.) of the part to keep it as close as possible to the process history of the coupons.
Overview[edit | edit source]
In the building block approach[1] (typically used in aerospace applications), the process begins by developing material allowables from coupon level tests such as those developed by the National Center for Advanced Materials Performance (NCAMP)[2]. Then progressively larger, more configured components and assemblies are analyzed, prototyped, tested and validated until the full-scale structure is realized and its behaviour and performance are fully understood at all levels of complexity. Ultimately then, the issue at hand is scaling. As outlined by Ilcewicz[3], there are two types of scaling that are important:
- size scaling, and
- production scaling
The building block approach is specifically developed to address size scaling in that it is intended to gradually scale up the physical dimensions and complexity of parts by providing design substantiation and validation at each level of size scaling. In this way, the relevant complexities and behaviours at all levels of size scaling are identified, understood and addressed. Production scaling refers to the scaling necessary to go from making a certain number of any part at a certain rate to making a different number of parts at a different rate. This is most often seen in the transition from prototyping to production. Both of these types of scaling can necessitate changes to the shape, tooling & consumables, and equipment (forming part of the MSTEP collection) that form a process step in the manufacturing processes, resulting in the risk of changes to part quality.
The quality of coupons are frequently interpreted as being superior to the material in the final parts. This can have many causes including:
- Different degree of cure — certain regions of the part may be under or over-cured, whereas it is easier to control cure in a coupon
- Size effects — larger structures are statistically more likely to have defects
- Residual stresses — The unloaded stress state of material in a part may be different than a coupon (owing to phenomena such as tool-part interaction and other causes of residual stress); resulting in an apparent change in strength properties that is actually due to a change in the initial unloaded stress state of the material
- New defects — Additional defects not seen in coupons are introduced as a result of the change in shape or size without effective mitigating measures
These quality issues are primarily due to the additional complexity of managing the material through the material deposition and cure stages of manufacture for a part that has a more complex shape. However, if the process steps are carefully controlled to avoid the creation of defects given the more complex shape, it is possible to improve the manufacturing outcomes of parts.
As explained in Systems Knowledge, composites processing is a complex interaction between material response, part shape and dimensions, tooling choices, and equipment behavior. Any change to the MSTEP collection may affect the manufacturing outcomes. When transitioning from making flat panel coupons to making configured parts it is presumed that you are keeping the material the same, and are changing the shape of the part. This may or may not involve changing the tooling (usually to correspond to a change in shape, but also for reasons of durability) or the equipment (perhaps an oven or autoclave of a different size and configuration, a press of a different size or configuration, or for room-temperature cure applications a different room in the factory). Changes to the tooling or equipment are also often consequences of production scaling, since it may not be possible to produce the larger quantities of parts needed during production using the same equipment and tools as those used for prototyping. Often times a manufacturer may also have several models of similar equipment (purchased at different times), but cannot economically restrict a given part to only being produced with a particular piece of equipment.
Since composites processing is a systems problem, and you are modifying the shape and potentially the tooling & equipment, it is important that you consider how these modifications affect outcomes related to:
- Thermal management
- Material deposition management
- Flow and consolidation management, and
- Residual stress and dimensional control management
Thermal management considerations[edit | edit source]
From a thermal management perspective, the first thing is to ensure that the material in the part sees a thermal history comparable to the coupons. This is a necessary but not sufficient requirement (you may still have other defects, such as voids and porosity, resin rich/poor regions, fibre wrinkling and waviness, and so forth).
Remembering the MSTEP framework, evaluate the thermal history relative to the panels used for manufacturing coupons. You can do this using:
- Thermal Simulation
- Thermal Test
- Combination of thermal simulation and test
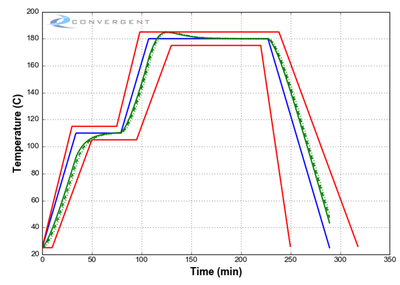
An example of thermal history evaluation using thermal simulation is shown in the figure on the right. In this figure it can be seen that as the air temperature (blue line) is increased, the part temperature (green lines) also increases, but with some lag owing to thermal resistances related to convection and conduction, as well as the thermal mass of the tool and part itself. Once the cure reaction takes hold, the heat of reaction adds energy directly into the composite part, resulting in an exotherm, which in this case causes the part temperature to exceed the applied air temperature. However, provided that the temperatures do not fall outside of the process specification (shown by the red lines), the quality of the part should be acceptable. Of course, it is preferable to keep the actual thermal profile as similar as possible to the thermal profile of the original coupons so that the process history and microstructural evolution is as similar as possible to the coupons. In practice it is impossible to achieve the exact same thermal history in all regions of the part (particularly through the thickness of thick parts), but steps outlined below can be taken to minimize discrepancies.
Effect of Shape[edit | edit source]
Link to effect of shape in a thermal management system
In all cases we need to be concerned about the effect of shape in a thermal management system. The shape of the part is representative of its geometry, including internal, external, local, and global features. The part geometry plays a key role in influencing heat transfer into and out of the part. Moreover, the dimensions and local features of the tool-part assembly can redirect and even block airflow in a convective heating system.
Change in shape can take many forms including:
- Change in part thickness
- Change in part size in contact with tool
- Change in configured shape of part (i.e. curvature instead of just flat coupons)
Change in part thickness[edit | edit source]
The change that will often have the most effect on thermal management is changes in part thickness. The through-thickness direction is often the dominant direction for heat transfer owing to its often smaller dimensions relative to the rest of the structure and larger thermal gradients. According to the conduction equation, \(q_x = -k\tfrac{\bigtriangleup T}{\bigtriangleup x}\), this results in higher heat flux through the thickness of the part.
For resin systems that require the application of heat to cure (see figures below), the temperature of the material in the middle of the through-thickness direction will initially lag further behind that of the exterior. As the cure process progresses however, the energy that is generated form the cure reaction can cause this thermal profile to invert for thick parts since heat cannot be removed fast enough. Whereas in thinner coupons it might be possible to keep the temperature difference between the surface and midplane of the part minimal; thicker parts will have larger differences in temperature during cure between the surface and midplane.
Most often, coupons are thinner than the parts that are ultimately manufactured, and so it is more likely that excess heat could cause issues with part quality. If the excess heat due to cure cannot be dissipated, then a local exotherm will occur, leading to local over-cure and possible heat damage.
10mm part | 50mm part |
---|---|
For resin systems that cure at room temperature (such as polyester resins), the more massive (thick) the part is, the more heat will be trapped within the part and the further the cure reaction will be advanced. If the part is large enough, the heat added by the part will dominate the cure reaction more so than the ambient air temperature. Due to this effect, a thicker part can actually reach the same degree of cure at a lower ambient air temperature as compared with a thinner part. This phenomenon is shown in the figures below. In particular, the right hand figure shows that at an ambient temperature of 20°C, an 8mm part reaches a DOC of 85%, whereas a 3mm part only reaches a final DOC of 76%. This difference becomes more stark the higher the ambient temperature. In contrast, at very low ambient temperatures, the thermal energy is not sufficient to significantly increase either the 3 or 8mm part to a high DOC. The green line represents the theoretical degree of cure of pure resin ignoring its mass and looking strictly at the specific (per mass) material properties. In other words, thickness of the resin layer is not taken into account. Hence why both the 3 and 8mm laminates display a higher final degree of cure as ambient air temperature increases.
Part temperature | Degree of cure |
---|---|
Change in part size in contact with tool[edit | edit source]
Owing to the dominant direction of heat transfer in a part being through-thickness. The change in part size in contact with the tool usually does not have a significant effect on thermal management considerations, but is more important to other considerations such as residual stress and dimensional control.
Change in configured shape of part[edit | edit source]
In convection heating systems, the largest effect of shape on thermal management considerations will likely be the influence of the shape on the airflow in the oven or autoclave as shown in the picture below. The interaction of the shape of the part (and its tooling) will alter the airflow and change local heat transfer coefficients (HTC). The change in local HTC alters the flow of heat into and out of the part locally. If the HTC is low, that region of the part will be slower to heat up initially, and slower to remove exothermic heat during cure. Conversely, regions with high HTCs will heat up more quickly, possibly resulting in higher exothermic temperatures, but will also be able to remove exothermic heat into the airflow more rapidly if the surface temperature of the part exceeds the air temperature.
Effect of tooling[edit | edit source]
Link to effect of tooling in a thermal management system
Tooling can be a major contributor to the thermal mass of the system and also the geometry that interacts with the equipment. Therefore it plays an important role in the thermal history of the part.
Tooling material and thickness[edit | edit source]
Increased tool thermal mass acts to damp out the effects of the exotherm caused by the heat of reaction of a curing laminate, but the magnitude of the effect is a complex interaction between part material and thickness, tool material and thickness, and the air temperature history (for equipment using convection). High tool thermal mass can also be an issue if it prevents certain areas of the part from ever reaching their necessary cure temperature for the required amount of time, and so this balance must be carefully considered, and the geometry of the tool designed appropriately based on the amount of composite material and heat transfer to the surrounding environment in certain regions. Both the tooling dimensions and the tooling material will affect the thermal mass.
Other material properties such as thermal conductivity and thermal diffusivity are also important. Thermal conductivity refers to how well the material transfers heat energy, while thermal diffusivity is a measure of the rate of this heat transfer, taking into account the object's conductivity and thermal mass. Tools with high thermal diffusivities, such as aluminum, show more uniform temperature distributions. Tools with low thermal diffusivity tend to show more severe temperature gradients across their surface.
The following table gives a qualitative comparison of typical tooling materials. Note that depending on the application, and local geometric features, thermal mass could be a benefit or a hindrance.
Tooling material | Cost | Durability | Weight | Thermal mass | Thermal conductivity | Coefficient of thermal expansion (CTE) | Thermal diffusivity |
---|---|---|---|---|---|---|---|
Invar | $$$ | Excellent | Heavy | High | Moderate | Low | Low |
Steels | $$$ | Excellent | Heavy | High | Good | Moderate | Moderate |
Composites | $ | Low | Light | Low | Low | Moderate | Low |
Aluminum | $$ | Good | Moderate | Low | Excellent | High | High |
A selection of physical and thermal material properties are also shown in the table below to give you a better idea of how different the various tooling materials are.
Tooling material | Density (kg/m3) | Specific heat capacity (J/kg-K) | Thermal conductivity (W/m-K) | Coefficient of thermal expansion - CTE (x10-6/°C) | Thermal diffusivity (x10-6m2/s) |
---|---|---|---|---|---|
Invar | 8000 | 515 | 11.0 | 0.6-1.5 | 2.67 |
Mild steel | 7850 | 510 | 55 | 11 | 13.7 |
Carbon-epoxy composite | 1580 | 870 | 0.7 (through-thickness) | -0.5 (in-plane) 22.5 (through-thickness) |
0.5 (through-thickness) |
Aluminum | 2710 | 896 | 167 | 23 | 68.9 |
Tooling shape[edit | edit source]
As discussed above in effect of shape, the shape of the tooling can also significantly alter how the part and tool interact with any equipment that uses convection as the method of heat transfer. Depending on your application, you may desire high convective heat transfer coefficients (usually the case for oven or autoclave curing, or room temperature curing of thick parts) or low convective heat transfer coefficients (often the case for room-temperature cure of thin parts or in low ambient temperature conditions).
Effect of equipment[edit | edit source]
Link to effect of equipment in a thermal management system
Generally speaking, changing the type of equipment (i.e. oven, autoclave, heated platens, room temperature, etc.) used for the thermal transformation step of a part to be different from that of the coupons is not an acceptable change as the boundary conditions and the applied temperatures around the part/tool will be drastically different than what was used for the coupons. However, it frequently occurs that a manufacturer may have several models of the same type of equipment (perhaps purchased at different times) with different geometries (size, configuration of internal baffles, etc.) and perhaps different heating methods (electric, gas, etc.), but cannot economically restrict a given part to only being produced with a particular piece of equipment.
When changing between equipment of the same type, two primary areas of focus should be:
- Temperature control
- Control of the interface between equipment and the tool-part assembly
Temperature control[edit | edit source]
Typically, accurate temperature control of the equipment itself (e.g. air temperature within an oven or autoclave) is often well controlled by the equipment. However, improper configuration of the equipment such as poorly tuned PID controllers, or improper pressure differentials could be a cause of temperature variations in the equipment. For example, ovens or autoclaves with poorly tuned PID's may oscillate significantly around the temperature set point, even when at steady state. If the oscillations occur slowly enough, the part temperature may also oscillate undesirably. The temperature may also undershoot or overshoot at the end of ramp segments, which can also contribute to poor thermal history in the part. Additionally, ovens that have a lower air pressure inside compared to the surrounding building can suck in cold air through gaps, resulting in local cold spots nears gaps (e.g. near doors). Ensuring a slight positive pressure and good sealing of gaps can prevent the introduction of air with the wrong temperature. In general, ensuring that the equipment is properly maintained to meet the original specifications of the manufacturer is important to preventing issues such as these.
In room-temperature cure applications, the building itself is the equipment. This can be very challenging in locations where the ambient outdoor temperature changes significantly with the seasons, or even within a day. Since the air temperature around the part is a very important boundary condition for room temperature cure parts, the environment should be controlled as best as possible with HVAC systems and/or staff should understand how the temperature will affect the timing of the process and how to mitigate the effect of temperature changes. For example, see the case study on troubleshooting of room temperature processes for large recreational and industrial parts.
Equipment and the tool-part interface[edit | edit source]
When changing between equipment of similar type, it is common to encounter changes to the interface between the equipment and the tool-part assembly. In convective heating systems this means changes to the airflow around the tool-part assembly and a resulting change in heat transfer coefficient.
Given that the goal is to keep the thermal history of the part as similar as possible to the coupons, this is not in and of itself an issue if it serves to cancel out effects from changes in part shape and tooling and results in a thermal history closer to that of the coupons. However, if the change in airflow combines with changes in part shape and tooling to make the thermal history of the part even more different than that of the coupons, then this is an issue. Ultimately, the combined response of the system composed of material, shape, tooling & consumables and equipment (MSTE), must be considered and adjusted so that the thermal response of the part is as close as possible to that of the coupons. This can be achieved through numerical simulation (see How to perform a numerical thermal profile) or experimental testing (see How to perform an experimental thermal profile).
Material deposition management considerations[edit | edit source]
Link to material deposition management
Content coming soon.
Flow and consolidation management considerations[edit | edit source]
Link to flow and consolidation management
Content coming soon.
Residual stress and dimensional control management considerations[edit | edit source]
Link to residual stress and dimensional control management
Content coming soon.
Diagnose[edit | edit source]
When considering how to troubleshoot a problem such as this, it is important to keep a fundamental concept in materials science in mind: The process history leads to microstructure evolution, which in turn determines mechanical and functional properties. Therefore, to obtain the same quality in final parts as we were able to achieve in the coupons, it is important to keep all parameters inside the part during manufacture as close as possible to how they were in the coupons during manufacture. Some key outcomes to look at are:
1. Degree of cure[edit | edit source]
Determine if your parts are showing signs of over-cure or under-cure. The following table lists some common methods of diagnosis for degree of cure:
Problematic outcome | Diagnosis method | Indicators |
---|---|---|
Under-cure | Visual Inspection |
|
Tactile inspection |
| |
Differential scanning calorimetry (DSC) |
| |
Fourier-transform infrared spectroscopy (FTIR) |
| |
Over-cure | Visual Inspection |
|
Tactile inspection |
| |
Differential scanning calorimetry |
| |
Fourier-transform infrared spectroscopy (FTIR) |
|
2. Thermal profile[edit | edit source]
Determine if the thermal profile of regions in your parts match the thermal profile experienced by your coupons. This can be achieved through numerical simulation (see How to perform a numerical thermal profile) or experimental testing (see How to perform an experimental thermal profile).
Remediate[edit | edit source]
Depending on your diagnosis, use your understanding of the systems approach to composites manufacturing in order to mitigate the quality issues by tuning the:
- Shape of the part-tool assembly,
- Tooling & consumables, and/or
- Equipment and how it interfaces with the part-tool assembly
Some common mitigation methods for common problematic outcomes are shown in the table below:
Theme | Problematic outcome | Mitigation strategy |
---|---|---|
Thermal management | Maximum temperature too high |
|
Minimum temperature too low |
| |
Uneven temperature/large thermal gradients across tool |
| |
Under-cured part |
| |
Over-cured part (thermally degraded/burned) |
|
Related pages
References
- ↑ [Ref] Composite Materials Handbook 17 - Polymer Matrix Composites; Materials Usage, Design and Analysis. 3. SAE International on behalf of CMH-17, a division of Wichita State University. 2012. pp. 4-1–4-62. ISBN 978-1-68015-454-2.CS1 maint: date and year (link)
- ↑ [Ref] "National Center for Advanced Materials Performance (NCAMP)". Retrieved 13 April 2021.
- ↑ [Ref] Ilcewicz, Larry B (1999). "Scaling crucial to integrated product development of composite aerospace structures. Part 1". 30 (3). doi:10.1016/S1359-835X(96)00116-9. Cite journal requires
|journal=
(help)CS1 maint: uses authors parameter (link)
About | Help |
An approach where risk is incrementally assessed in the scale-up of part size and complexity. Material and process (M&P) variabilities are evaluated at lower scales; While at higher scales, load paths and structural designs are verified. This approach involves three complementary engineering design activities:
- Material qualification
- Structural certification, and
- Production approval.
Degree of cure (DOC) is an indication of how far the chemical curing reaction (crosslinking process) has advanced in a thermoset resin.
DOC is defined with a number between 0 and 1 (or 0% and 100%) where 100% is a fully cured resin. It does not have to fully reach 100% for the resin to become solid or the part to be used. In some aerospace applications, resins are only cured to about 90%. Higher the degree of cure, higher the mechanical properties.
Any manufacturing and/or decision making activity that occurs during any stage of the development design cycle (e.g. conceptual design to production).
In the context of Knowledge in Practice, practice refers to the systematic use of science based knowledge to reduce composites manufacturing risk, cost, and development time.
A quantitative measure of how a material will respond to transient thermal conditions. It is defined as the ratio of thermal conductivity to the volumetric heat capacity of the material (density times the specific heat capacity).
Materials with large thermal diffusivity have a high thermal conductivity relative to their capacity to store energy (heat capacity) and will rapidly distribute the thermal energy throughout its volume and rapidly change temperature to reach the new equilibrium temperature.
Materials with small thermal diffusivity have a low thermal conductivity relative to their capacity to store energy (heat capacity) and will have a sluggish temperature response to a change in thermal conditions (large temperature lag). This is because it takes more energy per unit volume to change the temperature, and the low thermal conductivity means it takes longer to distribute the thermal energy throughout its volume.
Thermosets are a class of polymer that undergo polymerization and crosslinking during curing with the aid of a hardening agent and heating or promoter. Initially they behave like a viscous fluid. During curing, they change from viscous fluid to rubbery gel (viscoelastic material) and finally glassy solid.
If heated after curing, initially they become soft and rubbery at high temperatures. If further heated, they do not melt but decompose (burn)
Comes in two parts: part A (resin) and B (hardener). When mixed, curing reaction starts and is not reversible.
Examples include epoxy or polyester.

Welcome
Welcome to the CKN Knowledge in Practice Centre (KPC). The KPC is a resource for learning and applying scientific knowledge to the practice of composites manufacturing. As you navigate around the KPC, refer back to the information on this right-hand pane as a resource for understanding the intricacies of composites processing and why the KPC is laid out in the way that it is. The following video explains the KPC approach:
Understanding Composites Processing
The Knowledge in Practice Centre (KPC) is centered around a structured method of thinking about composite material manufacturing. From the top down, the heirarchy consists of:
- The factory
- Factory cells and/or the factory layout
- Process steps (embodied in the factory process flow) consisting of:
The way that the material, shape, tooling & consumables and equipment (abbreviated as MSTE) interact with each other during a process step is critical to the outcome of the manufacturing step, and ultimately critical to the quality of the finished part. The interactions between MSTE during a process step can be numerous and complex, but the Knowledge in Practice Centre aims to make you aware of these interactions, understand how one parameter affects another, and understand how to analyze the problem using a systems based approach. Using this approach, the factory can then be developed with a complete understanding and control of all interactions.
Interrelationship of Function, Shape, Material & Process
Design for manufacturing is critical to ensuring the producibility of a part. Trouble arises when it is considered too late or not at all in the design process. Conversely, process design (controlling the interactions between shape, material, tooling & consumables and equipment to achieve a desired outcome) must always consider the shape and material of the part. Ashby has developed and popularized the approach linking design (function) to the choice of material and shape, which influence the process selected and vice versa, as shown below:
Within the Knowledge in Practice Centre the same methodology is applied but the process is more fully defined by also explicitly calling out the equipment and tooling & consumables. Note that in common usage, a process which consists of many steps can be arbitrarily defined by just one step, e.g. "spray-up". Though convenient, this can be misleading.
Workflows
The KPC's Practice and Case Study volumes consist of three types of workflows:
- Development - Analyzing the interactions between MSTE in the process steps to make decisions on processing parameters and understanding how the process steps and factory cells fit within the factory.
- Troubleshooting - Guiding you to possible causes of processing issues affecting either cost, rate or quality and directing you to the most appropriate development workflow to improve the process
- Optimization - An expansion on the development workflows where a larger number of options are considered to achieve the best mixture of cost, rate & quality for your application.
To use this website, you must agree to our Terms and Conditions and Privacy Policy.
By clicking "I Accept" below, you confirm that you have read, understood, and accepted our Terms and Conditions and Privacy Policy.