Sandwich Panels - A325
Sandwich Panels | |
---|---|
Practice article | |
Document Type | Article |
Document Identifier | 325 |
Relevant Class |
Shape |
Tags | |
Prerequisites |
Introduction[edit | edit source]
Sandwich panels are typically constructed from a core material bonded between two thin, high strength face-sheets with adhesive or other bonding methods. Just like an I-beam, the core carries the shear loads while spacing the high strength material away from the neutral axis where the tensile or compressive loads are high in bending. This type of construction increases the moment of inertia and makes the structure more efficient in stiffness critical applications while very light weight. Because cores are continuously spread over the entire cross section, sandwich structures usually provides better torsional rigidity compared to I-beams. Sandwich structures can also offer functions such as energy absorption/damping radio frequency shielding and impact resistance.
Scope[edit | edit source]
This page will discuss the constituent materials, design, fabrication and quality control of sandwich panels. A sandwich panel can be assembled/manufactured by co-curing, co-bonding and secondary bonding. Brief descriptions of each process are as follows:
- Co-curing: both face sheets cure at the same time as the adhesive
- Co-bonding: bonding one precured face sheet to the core with an adhesive while the other uncured face sheet cures and adhesive bonds to the core at the same time
- Secondary bonding: bonding one or two precured composite face sheets to the core using adhesive. This term also applies to adhesive bonding aluminum face sheets to core
It is important to note that the usage of these terms are inconsistent within the composites industry. The implications of these terms may differ when applied to solid laminates, stiffened structures, or from company to company. For this section and other sandwich panels related topics on the Knowledge in Practice Centre, the terms are defined as above unless otherwise specified.
Significance[edit | edit source]
Sandwich panels are widely used across various industries. Properties such light weight, high stiffness, insulation and energy absorption are some of their most notable qualities. To successfully produce sandwich panels with good quality and performance, it is crucial to understand the elements, their properties and different manufacturing processes.
Prerequisites[edit | edit source]
Recommended documents to review before, or in parallel with this document:
Materials of sandwich panels[edit | edit source]
Cores[edit | edit source]
Core materials are available in a wide range of materials with variations within the core architecture for specific applications. Cores & inserts - A202 contains detailed discussions of different core materials. In addition to structural requirements, suitability of the material to match the required geometry should also be considered. Many core materials are rigid and limited in their ability to conform to curved geometry without splitting. Core machining or forming processes can be implemented with certain materials to obtain greater or more complex curvature and some cores (foam) can be moulded to complex shapes. However, the additional processing steps and cost can sometimes be avoided by either selecting a core material better suited for the required curvature, or by designing cored sections with limitations of the material in mind.
There are options to use semi-rigid foam, wood, or cork cores that have scores (partially through thickness slices) on one or both sides to allow for additional conformability. When using such products, it is important to always test the conformability of the core to the required curvature. Further considerations must be given to the increase in weight due to increase in resin-uptake in the scored cores. Refer to Cores & inserts for different types of cores and their properties.
Composite moulded parts manufactured with cores that do not conform to the geometry may lead to resin-rich areas, air voids, decreased mechanical properties, increased weight, and potential damage to the core.
Methods for producing core sections and assemblies should be considered during the design process. This could include processes such as forming, molding one-piece cores, CNC machining, assemble the cored sections from multiple pieces, or cutting and shaping the core by hand. Depending on the processes available, limitations in producing certain geometries should be considered. Simplified core geometry may be required in some cases to ensure that it can be processed consistently and cost effectively.
Face sheets[edit | edit source]
The same composite materials used to manufacture solid (monolithic) laminates can generally be used as sandwich face sheets. However, depending on different core materials, adhesives, and manufacturing process, the same composite material made as face sheets may have significantly different cosmetic appearance and mechanical properties compared a solid laminates. The suitability of a composite face sheet material can be evaluated by prototyping the sandwich panel, machining away the core and performing mechanical tests to obtain the face sheet properties. The face sheet properties are then compared to those of a solid laminate made from the same composite material. The knockdowns tend to be significant in compression.
Pre-preg with excess resin can be used as self-adhesive face sheets. The excess resin serves as adhesive that bonds to the core (forms fillets by the edges of the cells when bonding to a honeycomb core). However this is usually limited to light load applications where the core-to-face sheet bond strength is not critical.
Face sheet can present significant challenges for co-cured sandwich panels with open cell cores (such as honeycomb). Because the face sheets tend to drape into the cell during cure, dimpling/waviness can form and cause a loss of resin pressure in the composite laminate. Face sheet dimpling is a common issue when fabricating honeycomb sandwich panel will be discussed in the sections below.
Adhesives[edit | edit source]
Adhesives used for sandwich panels are typically film with uncured thickness of 0.075 mm to 0.38 mm. These film adhesives are typically thermoset polymers which require a thermal transformation (curing) process. If the adhesive is cured together with the (prepreg) face sheets, the adhesive must be compatible with the prepreg resin so that a third, weaker material is not created at the interface.
Film adhesives can be either supported or unsupported. Supported film adhesives have a loosely woven polyester, glass or nylon carrier or 'scrim' in them to facilitate easy handling and control the bond-line thickness. The carrier/scrim can be either embedded in the film adhesive or on the surface. If the carrier is on the surface, it is critical that the carrier faces the core for optimum bond strength. Unsupported film adhesives are typically extremely lightweight and reticulated when being used with honeycomb cores. During reticulation, the unsupported film adhesive is first applied to the honeycomb and heated so that the film adheres to the honeycomb cell edges. Pressurized hot air is then blown through the honeycomb cells causing the unsupported film adhesive to rupture at the center of the honeycomb cells. The resin surface tension will then cause the film adhesive to draw back, forming a bead of adhesive only on the edges of the honeycomb cells.
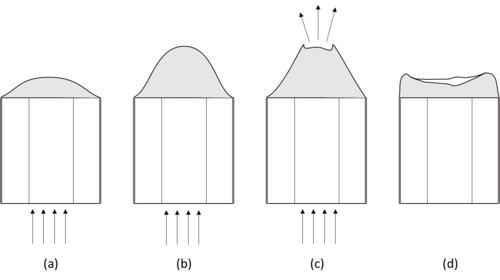
Because film adhesive typically gels before the matrix in the face sheet prepreg, in a co-curing scenario, the supported film adhesive may provide a surface for the face sheet to push against during the pre-gelation phase, allowing the development of some resin pressure. On the other hand, reticulated, unsupported adhesive films efficiently deposit the adhesive only on the edges of the honeycomb cells and saves the weight of excess adhesive away from the cell walls. Thus, the selection of supported vs unsupported film adhesive can depend on the product function and face sheet material system.
Adhesive used for co-cured sandwich panels with open cell cores (such as honeycomb) requires special considerations. The adhesive flow behavior (rheology) especially must to be precisely controlled. The adhesive needs to flow into the cells to form the fillets, but too much flow will leave little resin filleting the cell wall-to-face sheet interface. The adhesive running down the cell walls will contribute only to weight but not the bonding of the core and face sheets. Properties such as adhesive surface tension and viscosity play important roles for fillet formation.
Adhesives can be very sensitive to moisture exposure before bonding. Absorbed moisture can evaporate during cure and affect the core-to-face sheet bond strength. Some adhesive may also generate volatiles (outgas) during cure. The trapped gases can form blisters between the core and face sheets or pressurize the honeycomb cells to split/rupture in extreme cases.
Similar to any material evaluation, adhesive performance must be evaluated under all critical conditions. To evaluate the adhesive bond strength, it is common to use higher strength cores or less bonding area to further stress the bond. Flatwise tension and climbing drum peel are commonly used for the bond out-of-plane and peeling strength evaluation.
Surfacing and sealing[edit | edit source]
To improve the sandwich panel surface finish, surfacing films, resin wash or conventional fill and fair can be used. Surfacing films (sometimes a ply of fine weave glass prepreg) are similar to film adhesive in form and handling but with lower density. The surfacing film is typically cured with the face sheets and sanded afterwards. A resin wash involves smoothing and sealing the sandwich panel surface with a low viscosity resin. The sandwich panel is sometimes warmed to facilitate drawing resin into any surface pinholes/porosities.
Surfacing films, resin wash or conventional fill and fair can all require significant amount of labor and pose weight penalties to the product (fill and fair especially). Thus, sandwich panel surface finish and seal requirements should be seriously reviewed when developing a product and its manufacturing process.
Manufacturing of sandwich panels[edit | edit source]
The basic fabrication steps of a sandwich panel involves laying down the following material in sequence (from bottom up): tool side face sheet, adhesive, core, adhesive, bag side face sheet, release film, breather/bleeder, bagging assembly. See figure below.
Sandwich panels processing pressure[edit | edit source]
To avoid core movement or deformation, processing pressure for sandwich panels are generally lower than that of solid laminates. For example, honeycomb sandwich panels are usually cured in the range of 15 to 50 psig[1]. Depending on the core material and strength, even vacuum pressure alone can cause core movement or deformation. The designer can limit the vacuum pressure (to 8-10 inches of Hg for example) in those case.
Processing (especially co-curing) honeycomb sandwich panels in an autoclave requires special considerations. While the autoclave pressure can be around 40 psi, the pressure in the honeycomb cell may only be a few psi or even zero. As face sheets droop into the honeycomb cells, the resin pressure in the face sheet and adhesive is also close to zero which can cause porosity and low levels of consolidation. For this same reason, processing honeycomb sandwich panels in an autoclave is also more sensitive to bag leaks than solid laminate. The autoclave pressure entering a honeycomb cell can literally blow the core apart.
Honeycomb Sandwich panel potting and closeouts[edit | edit source]
Cells of the honeycomb sandwich panels can be selectively filled and reinforced with foam or other materials, i.e. "potting" for the following reasons:
- local reinforcement for product assembly with fasteners
- prevent core crush during processing
- locally increase surface area for bonding
- stabilize the honeycomb cell walls for machining
- achieve thermal and acoustic insulation properties
Depending on the application, foam of various densities or epoxy filled with chopped fibre can be used to fill the honeycomb cells.
Honeycomb sandwich panels require special closeouts at the edges to prevent potential water ingression. Various types of closeouts and their tradeoffs add to the complexity of honeycomb sandwich panel design and manufacturing.
Thermal management for sandwich panels[edit | edit source]
The selection of appropriate core materials and configurations will be tied to requirements and conditions of the manufacturing process. From a thermal management perspective, cores typically insulate the tool side and bag side face sheets to some extend due to their low thermal conductivity. Hence it complicates the system level problem involving the material, shape, tooling and equipment during the thermal transformation step. For example, see Development of a cure cycle for a tapered sandwich laminate fuselage panel.
Material deposition and consolidation management for for sandwich panels[edit | edit source]
Core locations in a component should be easy to identify to allow for rapid and consistent application during the material deposition step. This may be assisted by the use of projection systems to show core locations on the part surface, core location templates, or indexed from geometry in the tool. In addition to the initial location and positioning, the core must be able to stay in place throughout the manufacturing process. With some manufacturing processes such as prepreg processing where the composite material is somewhat tacky, this can be relatively easy to maintain with the application of a compaction bag. In manufacturing processes where the core material is up against dry fabric during the layup stage, maintaining correct core position can be more difficult. This can apply to processes such as resin infusion as well as prepreg manufacture using single-side impregnated material. In some situations, it may be beneficial to include features in the cored sections to assist in maintaining position during layup, rather than for structural purposes.
If the manufacturing process being used includes the application of pressure (vacuum or positive hydrostatic pressure) the impact of processing pressure needs to be considered when designing the core and core chamfers. On core chamfers, external pressure will apply force components in both the vertical and horizontal directions, with greater horizontal components acting on steeper chamfer angles. This can lead to the core crushing in-plane during processing. This can be mitigated by using shallower chamfers, higher density core or stabilizing materials in the chamfer region, or using tooling strategies to reduce the in-plane force.
When using core materials in a resin infusion process, consideration should be made to allow sufficient resin flow on either side of the core material. In some situations this may be accomplished by scoring the core to allow for resin pathways along the core surface if the infusion is being completed in a manner which will allow for the edges of the core to be accessed. Alternatively, perforations in the core may be needed to allow for resin to pass through the core thickness. Certain core materials such as honeycomb have very different properties in the through-thickness direction compared with in-plane directions. The availability of different core configurations will vary by supplier, core material, and thickness, making it important to assess the options and suitability for the manufacturing process during the design phase.
Manufacturing outcomes and quality management of sandwich panels[edit | edit source]
Face sheet dimpling[edit | edit source]
A common issue during co-curing honeycomb sandwich panels (face sheets are cured at the same time as the adhesive) is face sheets dimpling. See figure on the right. The honeycomb core pattern can telegraph to the face sheet on either the bag side or the tool side of the sandwich panel for various reasons. In general, the thinner the face sheets and larger the honeycomb cell size, the easier it is for the face sheet to droop into the unsupported areas on the honeycomb cells. The dimpled face sheet may also exhibit resin starvation and increased surfaced porosity (especially on the tool side).
Face sheet dimpling on the tool-side surface can sometimes be caused by poorly-designed cores. This defect may be due to several factors such as:
- non-conforming core geometry that applies increased pressure along the core edges on the laminate
- stiff and sharp core edges with insufficient transition region that applies pressure along the core edges to the laminate
- resin-rich regions around transitions to cored areas that result in local areas of high shrinkage during cure
It is not always possible to eliminate print-through on a component, but a designer can attempt to mitigate its effect by designing the core such that the core edges are positioned directly over top of a geometric feature, such as a bend, surface transition, or a corner radius.
Other manufacturing outcomes[edit | edit source]
Other manufacturing outcomes of a sandwich panel can include:
- Face sheet porosity level - high face sheet porosity can be caused by low resin pressure or other manufacturing setup/parameters
- Adhesive fillet health - one-sided fillets, no fillets, small fillets, uneven fillets or adhesive running down the cell wall are non-ideal manufacturing outcomes for adhesive fillets. Few potential causes include inappropriate adhesive material selection, excessive adhesive out time, adhesive moisture absorption or other manufacturing setup/parameters
- Adhesive porosity level - high adhesive porosity can be caused by low resin pressure, adhesive curing before volatiles/outgassing was able to escape or other manufacturing setup/parameters
- Core movement - migration, crushing or splitting can be caused by high processing pressure or other manufacturing setup/parameters
Related pages
Page type | Links |
---|---|
Introduction to Composites Articles | |
Foundational Knowledge Articles | |
Foundational Knowledge Method Documents | |
Foundational Knowledge Worked Examples | |
Systems Knowledge Articles | |
Systems Knowledge Method Documents | |
Systems Knowledge Worked Examples | |
Systems Catalogue Articles | |
Systems Catalogue Objects – Material | |
Systems Catalogue Objects – Shape | |
Systems Catalogue Objects – Tooling and consumables | |
Systems Catalogue Objects – Equipment | |
Practice Documents | |
Case Studies | |
Perspectives Articles |
References
- ↑ [Ref] Campbell, F.C. (2004). Manufacturing Processes for Advanced Composites. Elsevier. doi:10.1016/B978-1-85617-415-2.X5000-X. ISBN 9781856174152.CS1 maint: uses authors parameter (link) CS1 maint: date and year (link)
About | Help |
Thermosets are a class of polymer that undergo polymerization and crosslinking during curing with the aid of a hardening agent and heating or promoter. Initially they behave like a viscous fluid. During curing, they change from viscous fluid to rubbery gel (viscoelastic material) and finally glassy solid.
If heated after curing, initially they become soft and rubbery at high temperatures. If further heated, they do not melt but decompose (burn)
Comes in two parts: part A (resin) and B (hardener). When mixed, curing reaction starts and is not reversible.
Examples include epoxy or polyester.
Pre-impregnated (prepreg) material refers to fibre that is already combined with resin. It is the most common material form used in aerospace.
During prepreg production, (e.g. fibres are run through a resin bath), prepreg is heated and partially cured to B Stage (< 5 % degree of cure). Thermoset prepregs (e.g. epoxy prepreg) have to be kept in a freezer at around -20 °C. At room temperature, the epoxy starts to cure.
In composites processing, viscosity is an indicator of how easily the resin matrix will mix with the reinforcement and how well it will stay in place during processing. The lower the viscosity, the more easily resin flows. Resin viscosity ranges considerably across chemistries and formulations.
By scientific definition, viscosity is a measure of a material’s resistance to deformation. For liquids, it is in response to imposed shear stresses.

Welcome
Welcome to the CKN Knowledge in Practice Centre (KPC). The KPC is a resource for learning and applying scientific knowledge to the practice of composites manufacturing. As you navigate around the KPC, refer back to the information on this right-hand pane as a resource for understanding the intricacies of composites processing and why the KPC is laid out in the way that it is. The following video explains the KPC approach:
Understanding Composites Processing
The Knowledge in Practice Centre (KPC) is centered around a structured method of thinking about composite material manufacturing. From the top down, the heirarchy consists of:
- The factory
- Factory cells and/or the factory layout
- Process steps (embodied in the factory process flow) consisting of:
The way that the material, shape, tooling & consumables and equipment (abbreviated as MSTE) interact with each other during a process step is critical to the outcome of the manufacturing step, and ultimately critical to the quality of the finished part. The interactions between MSTE during a process step can be numerous and complex, but the Knowledge in Practice Centre aims to make you aware of these interactions, understand how one parameter affects another, and understand how to analyze the problem using a systems based approach. Using this approach, the factory can then be developed with a complete understanding and control of all interactions.
Interrelationship of Function, Shape, Material & Process
Design for manufacturing is critical to ensuring the producibility of a part. Trouble arises when it is considered too late or not at all in the design process. Conversely, process design (controlling the interactions between shape, material, tooling & consumables and equipment to achieve a desired outcome) must always consider the shape and material of the part. Ashby has developed and popularized the approach linking design (function) to the choice of material and shape, which influence the process selected and vice versa, as shown below:
Within the Knowledge in Practice Centre the same methodology is applied but the process is more fully defined by also explicitly calling out the equipment and tooling & consumables. Note that in common usage, a process which consists of many steps can be arbitrarily defined by just one step, e.g. "spray-up". Though convenient, this can be misleading.
Workflows
The KPC's Practice and Case Study volumes consist of three types of workflows:
- Development - Analyzing the interactions between MSTE in the process steps to make decisions on processing parameters and understanding how the process steps and factory cells fit within the factory.
- Troubleshooting - Guiding you to possible causes of processing issues affecting either cost, rate or quality and directing you to the most appropriate development workflow to improve the process
- Optimization - An expansion on the development workflows where a larger number of options are considered to achieve the best mixture of cost, rate & quality for your application.
To use this website, you must agree to our Terms and Conditions and Privacy Policy.
By clicking "I Accept" below, you confirm that you have read, understood, and accepted our Terms and Conditions and Privacy Policy.